Digitalization is revolutionizing aerospace manufacturing, marking a significant shift from traditional methods to a future where digital technology leads the way. At its core, digitalization in aerospace harnesses digital technologies to transform every aspect of how aircraft components are designed, produced, and managed. This isn’t just an upgrade of tools or processes, but a complete reimagining of manufacturing, promising unprecedented efficiency, innovation, and precision.
Gone are the days when aerospace production lines solely depended on manual efforts and time-tested, linear processes. Today, the industry is navigating towards digital-first practices, where technologies like Computer-Aided Design (CAD), 3D printing, the Internet of Things (IoT), and Artificial Intelligence (AI) are unlocking new possibilities. For industry leaders like Carr Lane Mfg., shifting toward digitalization is a strategic move that is redefining the future of aerospace manufacturing, from aircraft components to the tools that build them.
In this article, the experts at Carr Lane Mfg. explore how digitalization is changing the industry, the impact that this shift will have on tooling and manufacturing, and how Carr Lane Mfg. is utilizing new technologies to optimize production and boost product quality.
The Core Components of Digitalization in Aerospace Manufacturing
Imagine walking through a state-of-the-art aerospace manufacturing facility: to your left, a designer fine-tunes a component on a high-resolution CAD system; to your right, a 3D printer hums quietly as it lays down layers of a high-strength polymer for a prototype. This is the new reality of aerospace manufacturing, where digital tools and processes collide to create an innovative and efficient operation.
Digitalization has introduced many new technologies, from Computer-Aided Design (CAD) and industrial 3D printing for precise prototyping to the Internet of Things (IoT) and sensors for lights-out manufacturing operations. Carr Lane Mfg. uses many of these solutions to create the highest-quality, most reliable components for aerospace applications, including the recent addition of galvanic corrosion-resistant coatings for additional durability.
Digital Design and Simulation
Computer-Aided Design (CAD) and Computer-Aided Engineering (CAE) have revolutionized the way aerospace components are conceptualized and brought to life. CAD allows engineers to craft detailed and accurate designs of complex components with a level of precision that was previously unachievable. With CAD, aerospace manufacturers can move from concept to production seamlessly, ensuring every detail of the design is perfected before a single piece of metal is cut.
Carr Lane Mfg. uses CAD technology in both assembly and production planning, offering real-time design solutions to clients to ensure components meet the exact requirements specified by OEMs and vendors. This capability is especially crucial in aerospace, where every component must meet stringent specifications. Carr Lane Mfg.'s approach to CAD enables clients to select the precise coatings and metal types of Captive products for their unique applications, ensuring optimal performance and compatibility.
CAE tools provide simulations that allow engineers to test and refine their designs in a virtual environment. This helps engineers identify and address potential issues long before physical prototypes or products are created, saving significant time and resources. By simulating different conditions and scenarios, engineers can ensure that the design is not only manufacturable but will perform as expected under the harsh conditions experienced in aerospace applications.
Additive Manufacturing (Industrial 3D Printing)
Additive manufacturing, or industrial 3D printing, has ushered in a new era of manufacturing. Unlike traditional manufacturing methods, which remove material to shape a part, additive manufacturing builds parts layer by layer from the ground up, fusing each layer together with a precise layer to create a complete component.
One of the most compelling benefits of additive manufacturing in aerospace is the potential for “lights-out” production. This concept refers to the ability to operate manufacturing equipment, including 3D printers, overnight or for extended periods of time without human intervention. Through a combination of additive manufacturing and automation technologies, aerospace manufacturers can keep production running 24/7. This not only accelerates production timelines but also significantly reduces labor costs and the possibility of human error, ensuring consistent quality and output.
Carr Lane Mfg. has embraced additive manufacturing, leveraging it for both prototyping and the production of specific aerospace components. This approach allows for rapid iteration and testing of prototypes, greatly reducing the development time for new products. Beyond prototyping, Carr Lane Mfg. has successfully integrated additive manufacturing into the production of critical aerospace components, such as key inserts and grippers.
Sensors and Cycle Monitoring
Advanced sensors play a pivotal role in real-time cycle monitoring, enabling continuous, automated monitoring of production processes to ensure operations run smoothly around the clock without constant human oversight. By harnessing the power of sensors, aerospace manufacturers can gather detailed, real-time data on every aspect of the manufacturing cycle. From adjusting machine parameters on the fly to ensure optimal performance, to predicting when maintenance is needed before a breakdown occurs, sensors make it all possible.
A prime example of how Carr Lane Mfg. is enabling real-time machine monitoring can be seen in our air rest buttons. These innovative components enable engineers to use pneumatic position control to detect the proper loading of a workpiece into the machining fixture. When the workpiece is correctly placed on the air rest button, the precision floating plunger fully retracts into the threaded body, sealing off airflow and increasing the overall pressure of the system. This pressure value can be read and monitored using an analog or digital pressure sensor, which can then be tied into a PLC or control system for peak productivity and real-time monitoring.
Augmented Reality (AR)
Augmented Reality (AR) overlays digital information onto the real world, allowing for an interactive experience with virtual aircraft components that fosters a comprehensive understanding of complex aerospace systems. AR also allows designers and engineers to see a full-scale model of a component or system as it would appear in reality, enabling better decision-making and more efficient design iterations.
Carr Lane Mfg. uses AR technology to pinpoint precisely where and how parts will integrate into the broader component system. This ensures a flawless fit and function for critical aerospace components, such as the mounting brackets we produce for military aerospace applications such as pilot headsets.
How the Digital Transformation Impacts Aerospace Tooling and Manufacturing
The digital transformation in the aerospace industry is fundamentally changing how aerospace engineers work and how components are manufactured. Here’s how these technological advancements are reshaping aerospace tooling and manufacturing:
- Precision and Customization: Digital technologies can create components with unparalleled accuracy while adhering to the strictest aerospace standards. Additionally, with CAD and CAE, customization options are vast, allowing for parts to be tailored to specific applications.
- Speed and Efficiency: Digital tools can significantly reduce the time from design to production, streamlining the manufacturing cycle. With automated processes and AI-driven optimizations, aerospace manufacturers can use resources and manpower more efficiently, accelerating production rates.
- Cost Reduction: By minimizing the need for physical prototypes through simulations, the costs associated with prototyping are drastically lowered. Digital inventory management systems can also optimize stock levels, reducing excess inventory and associated costs.
- Enhanced Quality Control: Advanced analytics and artificial intelligence provide deep insights into manufacturing processes, identifying potential quality issues before they occur. Real-time monitoring and predictive maintenance strategies can also result in fewer defects and enhanced product reliability.
- Sustainability: Digital innovations drive sustainable manufacturing practices, significantly reducing the industry’s environmental footprint. Through precise material usage and waste minimization, digital solutions contribute to more eco-friendly manufacturing processes.
- Lights-Out Manufacturing: Digitalization enables manufacturers to implement fully automated, lights-out manufacturing processes that can run without human intervention, often operating overnight to boost production volume and efficiency. Carr Lane Mfg. showcases the power of lights-out manufacturing with our on-site robot work center (shown in the images below), which autonomously produces alignment pins and hand knobs.
- Supply Chain Optimization: Integrating digital tools into aerospace supply chain operations enables real-time material and component tracking for increased efficiency. Additionally, enhanced collaboration platforms ensure seamless communication and coordination among suppliers, manufacturers, and customers, optimizing the entire supply chain.
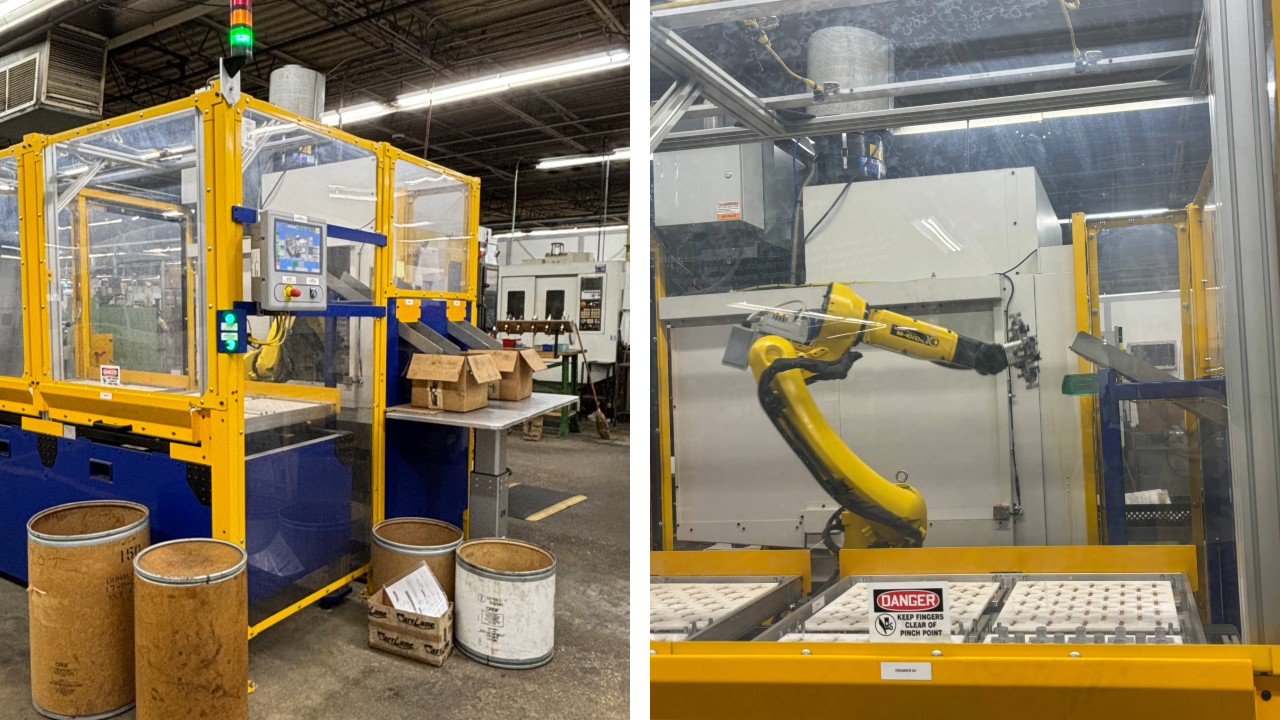
The Challenges of Aerospace Digitalization
While the digital transformation in aerospace manufacturing opens up a wide realm of possibilities, it also presents a set of challenges that manufacturers must navigate. These challenges, ranging from financial and technical to operational, can pose significant barriers to entry, especially for smaller manufacturers and machine shops.
The initial financial investment required to integrate digital technologies into manufacturing processes can be substantial, making it the primary challenge of digitalization. For many smaller operations, this investment represents a difficult obstacle, with concerns about the return on investment (ROI) and the impact on cash flow. However, this upfront cost can lead to substantial long-term savings through increased efficiency, reduced waste, and lower operational costs. The integration of advanced technologies can also be technically complex, requiring specialized knowledge and skills that may not be present within your current workforce.
Despite these challenges, there are specific strategies that aerospace manufacturers can use to mitigate risks:
- Invest in comprehensive workforce training.
- Adopt a phased approach to technology integration.
- Form partnerships with technology providers, component manufacturers, and industry experts.
- Explore government and industry grants for additional funding.
The Future of Aerospace Manufacturing with Digitalization
Aerospace manufacturing is moving toward a future where digital technologies are central pillars of manufacturing operations. The integration of innovative technologies like Artificial Intelligence (AI) and Machine Learning (ML), along with the development of comprehensive digital ecosystems, is poised to redefine what’s possible in the industry.
The application of AI and ML in aerospace manufacturing is expected to continue to grow, offering unprecedented insights into efficiency, predictive maintenance, and design optimization. These technologies will allow aerospace manufacturers to create smarter processes that can adapt in real-time to changing conditions and demands. We’re also expecting to see more collaborative platforms in the cloud, data-sharing applications, and integrated digital workflows that will streamline communication, design, production, and supply chain management. These ecosystems will foster a level of collaboration and efficiency that is currently unimaginable, breaking down silos between different stages of the manufacturing process and even between different companies.
Revolutionize Your Aerospace Manufacturing Operation with Carr Lane Mfg.
Digitalization in aerospace manufacturing is revealing a future where efficiency, innovation, and precision are not just goals but realities of everyday production. The transformative power of technologies like Computer-Aided Design (CAD), Additive Manufacturing, Real-Time Sensors, and Augmented Reality (AR) is reshaping the industry, setting new benchmarks for what can be achieved.
Carr Lane Mfg. is committed to innovation, adopting cutting-edge digital technologies to ensure that our products meet the rigid standards of the aerospace industry. From precision-engineered alignment pins to customized captive products, Carr Lane Mfg. offers a wide range of products that provide unmatched durability, efficiency, and resistance in aerospace applications.
Whether you are seeking to optimize your manufacturing processes, enhance the quality of your products, or explore new avenues of innovation, Carr Lane Mfg. is here to help. By partnering with Carr Lane Mfg., you are not just preparing for the changes that digitalization brings — you are stepping into a future where the possibilities are limitless. We encourage you to browse Carr Lane’s extensive product catalog and connect with one of our experts to discover the best tooling solutions for your specific aerospace application.